The Handpan is a musical instrument who do not produce large production lines. The making of a Handpan takes time and requires not "manufacturers" but true "artisans".
Manufacturing a Handpan is an art, and giving it its resonance, to offer him his range, ensure its harmony in some chords melodious requires the greatest dexterity.
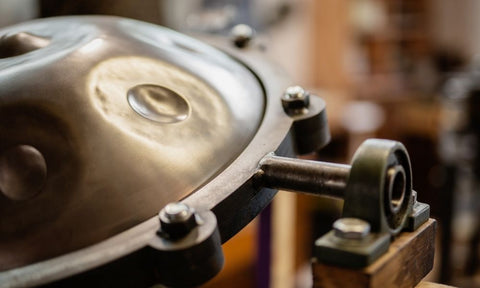
How is this instrument with such an angelic sound born? What are the secrets of making a Handpan? Immersion in the workshops of Handpan makers, whose works are available for purchase at Zenapan.
Also to read: Quelle est l’origine du Handpan ?
1. Make a Handpan by sculpting a sheet of steel
The first step of the manufacturing of a Handpan The choice of steel sheet is based on. There are two different types of steel:
- L’nitrided steel (DC04),
- L’stainless steel.
Handpans are often made with nitrided steel, so we will start by discussing this one before looking at the others.
a. Theacier nitruré
Theacier nitruré est un acier traité par thermochimie. Comme le nom de cette technique l’indique, la nitruration repose sur la chauffe de l’acier, auquel est injecté de l’azote.
This nitrogen injection has two main functions:
- It strengthens the Hang drum,
- It protects it from rust.
The use of this type of steel does have some drawbacks. The first is that nitriding does not prevent rust from appearing but slows it down. Therefore, it is important to take special care of your instrument.
The second is that nitriding changes the length of sound of the instrument. The nitrided Handpans, which today make up the vast majority of instruments, develop a sound whose sustain (called sustain) in English is shorter.
The sound of nitrided steel Handpans is also changed. It becomes more clay-like, and is often referred to as "ceramic" by the musicians.
On the contrary, nitriding allows for a louder sound, which greatly facilitates the outdoor gameIt also helps to maintain the instrument granted for years.
b. Stainless steel
Stainless steel (stainless steel) is sometimes used by manufacturers because it does not rust. It therefore does not require themaintenance what imposes a Handpan made of nitrided steel.
The manufacturing of a Handpan stainless steel It also guarantees him greater freedom of play locations. That is to say, it can be played anywhere, whether by the sea or in humid regions.
The sound quality is also different. The duration of the note is longer, its melody deeper. However, the sound is much quieter. It is therefore much more of a interior instrument.
However, the Handpans made of stainless steel have a very big flaw: their non-resistance to heat. Played under a summer sun, or forgotten in the heat, and your Handpan disagrees.
Either it will return to its original tuning once cooled, or it will be necessary to have it retuned by the manufacturer.
Succumb to the magic of the hang drum sound! Discover our original handpans made of steel, forged with passion for an unforgettable musical experience.
2. Hammering the structure to form the dome
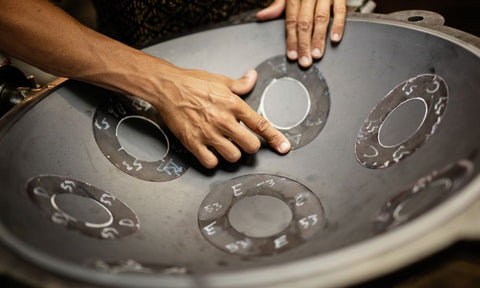
The creation of a handpan, this enchanting musical instrument, is an art that requires precision and expertise. Here is an overview of the meticulous process involved:
- Formation of the Dome
A sheet of steel is meticulously bolted onto a support. Through expert hammering, it is transformed into a dome, symbolizing the heart of the handpan. This process is only completed when the shape is perfectly rounded and flat.
- Marking and Initial Tuning
The precise location of the notes is marked inside the dome. The artisan then proceeds with the initial tuning, sculpting delicate curves that will bring the sound of the handpan to life.
- Heat Treatment
To reinforce its structure, the dome is heated to 400°C for about two hours, a crucial step to ensure the durability of the handpan.
- Base Training
A second sheet of steel is prepared and hammered until it forms the base of the instrument. It is finally joined to the upper part, completing the physical structure of the handpan.
This process, combining tradition and innovation, reflects the complexity and beauty of handpan music, making each instrument unique. From original handpans to modern creations tuned to 432 hertz for the relaxation or to 440 hertz for the composition, each step is crucial to achieving sound excellence.
Here is a video preview of how a handpan facilitates meditation and relaxation:
You enjoyed this celestial sound? If so, let yourself be enchanted by the sound of our handpans right now! Explore our collection unique instruments, the result of exceptional artisanal know-how.
3. Thermochemical treatment by nitriding
The nitriding process is a crucial step in the manufacturing of the handpan, ensuring the instrument's longevity and exceptional sound quality.
Here are the key points of this treatment:
- Treatment Temperature The steel is exposed to a temperature of around 500°C, optimizing the efficiency of nitriding.
- Nitrogen Projection Nitrogen is carefully sprayed onto the surface of the instrument, thereby strengthening the metal deeply and increasing its resistance to corrosion.
- Increased resistance : The handpan becomes significantly more resilient to rust, essential for musical instruments exposed to various conditions.
- Improved stability : This technique ensures the handpan's ability to stay in tune over the long term, an asset for musicians seeking unwavering reliability in their instrument.
Nitriding thus transforms the handpan, not only by preserving it from the elements but also by perfecting its sound and durability, making each handpan a true masterpiece of musical craftsmanship.
4. The final tuning of the handpan
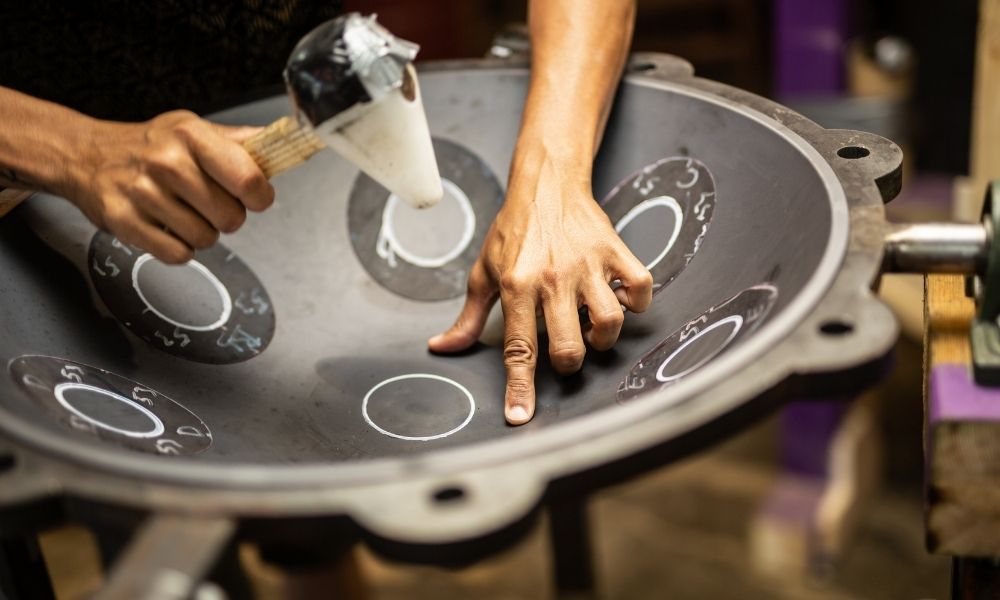
Tuning a steel hang drum requires great precision in handling the hammers. Each note is achieved through a more or less deep shape. Precision is therefore essential in obtaining a correct and precise sound.
Any frequency can be obtained, but generally speaking, handpans have a frequency of 440Hz, in accordance with classical Western instruments. This allows steel pan percussionists to perform in concerts with other instruments.
The importance of precision in thetuning of the hang drum Rest in the necessity of not creating interference. That is to say, a crossing zone between two notes, which would have the effect of creating false notes. A bit like if you were rubbing two strings at the same time on a violin.
This is why the majority of Handpans do not have more than ten notes, in order to avoid these interferences, and thus to not lose in musical quality.
5. Summary of the key steps in the manufacturing of the Handpan
Step | Description |
---|---|
Selection of steel | Choice of nitrided steel for its resistance and sound quality. |
Dome hammering | Dome formation by precise hammering on a support. |
Marking and first tuning | Marking the locations of the notes and initial tuning to form the sound curves. |
Heat treatment | Heating the dome to 400°C to strengthen the steel structure. |
Foundation training | Hammering a second sheet of steel to create the base, then assembling with the dome. |
Final agreement | Meticulous adjustment of notes for a perfect harmony. |
Finishes | Application of finishes, such as oiling or painting, to protect and enhance the instrument. |
Offer yourself an unforgettable musical experience! Explore our collection unique handpans, crafted with passion and expertise.
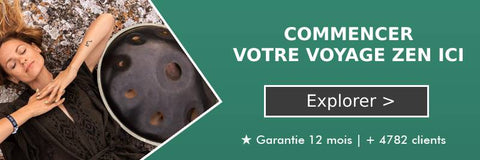
In conclusion
La manufacturing of the steel hang drum is a delicate art that combines technical precision and musical passion. Each step, from the initial hammering to the final tuning, reflects exceptional craftsmanship, transforming a simple sheet of steel into an instrument with celestial soundsThis alchemy between materials and artisanal mastery creates not only a musical instrument but also a source of well-being and inspiration for musicians and listeners from around the world.
Ready to compose your own symphony? Discover our collection of handpans now in clicking here and enjoy magical sound at your fingertips!
Frequently Asked Questions
1. What type of steel is used to make a handpan?
Nitrided steel is commonly used for its corrosion resistance and its ability to produce a rich and pure sound, essential for the sound quality of the handpan.
2. How long does it take to make a handpan?
The creation of a handpan can vary, generally requiring between 40 and 50 hours of meticulous work. Each step, from hammering to tuning, is carried out with exceptional attention to detail.
3. What makes each handpan unique?
The uniqueness of each handpan lies in its manual tuning process and the subtle variations in the hammering of the steel. This gives each instrument its own character and distinct timbre.
4. Why are handpans often expensive?
The high price of the handpan reflects the complexity of its manufacturing, the time dedicated to its creation, and the expertise of the artisan. Each handpan is a handmade musical work of art.
5. Can the notes of a handpan be customized during its manufacture?
Yes, the customization of notes is possible and common. Future owners can choose the scale of the handpan according to their musical preferences, allowing for a unique personal expression through their music.